Back-to-Basics: Structure Zone Models for Thin Films
Dr. Peter Martin
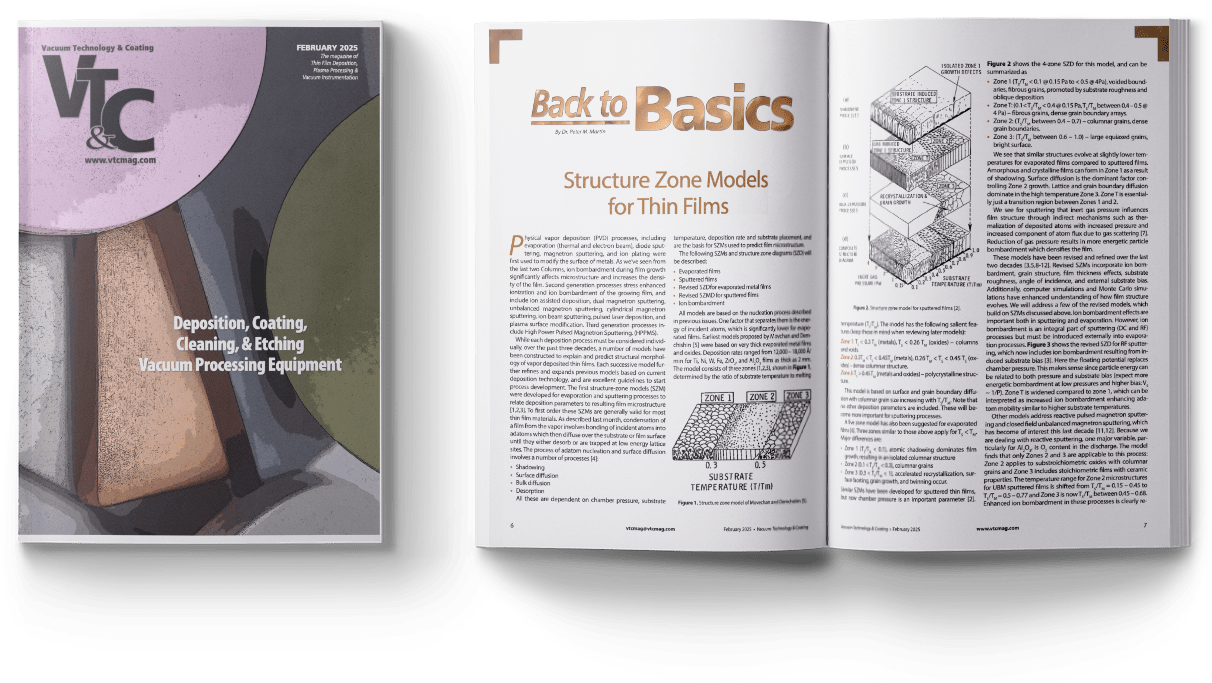
A research team has developed a printing-based selective metal film deposition technique that enables the facile and fast fabrication of high-performance soft electronic devices and circuits in various forms. (click for more)
Requirements for physical vapor deposition (PVD) coating equipment vary between R&D systems and production tools. However, in either case having a definition of the coating machine requirements is paramount to arrive at PVD equipment costs. (click for more)
Researchers at Oak Ridge National Laboratory have developed a new automated testing capability for semiconductor devices, which is newly available to researchers and industry partners in the Grid Research Integration and Deployment Center, or GRID-C. (click for more)
Berkeley Lab-led project part of new DOE Microelectronics Science Research Centers that are focused on basic research to transform the efficiency of microelectronics (click for more)
Since 2000 Vacuum Technology & Coating Magazine has been the industry's leading source for the latest articles, news, and product and service information. Below we describe some of the terms that you will find in a typical issue of VT&C.
Vacuum Coating (Vacuum Deposition and Thin Film Deposition) is the process of depositing a film or other material atom by atom or molecule by molecule onto a surface in a low pressure environment or vacuum.
Physical Vapor Deposition or PVD refers to vacuum deposition methods which involve the material (which is being deposited) going from a condensed phase to a vapor phase and then to a thin film condensed phase. Sputtering and evaporation are common PVD processes.
Sputtering refers to a type of process used to deposit thin films and employs a plasma to bombard and eject atoms from a target source.
Evaporation refers to the heated source material being evaporated in a vacuum. Vacuum allows vapor particles to travel directly to the target object, where they condense back to a solid state. (called a Deposition Source) refers to a type of process used to deposit thin films and employs a plasma to bombard and eject atoms from the target source (called a Deposition Source).
Vacuum Hardware refers to the types of hardware and components that are used in the vacuum process. There are many types of hardware used in this process, some examples are flanges, fittings, seals, valves, and chambers.
Thin Film Metrology involves determining the optimal thickness, composition and/or condition of a coating through various techniques and mathematical calculations.
Gas Analytical Systems are used in the analysis of residual gases within a low pressure environment or vacuum.
Vacuum Pumps are devices that remove gas atoms and molecules for the purpose of leaving behind a partial vacuum. Some examples of types of vacuum pumps are rotary vane pumps, diaphragm pumps, and scroll pumps.
Every issue of VT&C includes a product showcase focused on a specific topic relevant to Vacuum Processing, please see our editorial calendar which lists the topic for each issue.