Vacuum Advances in Biotechnology: Combating Highly Pathogenic Bacteria
Dr. Megha Agrawal and Dr. Shyamasri Biswas
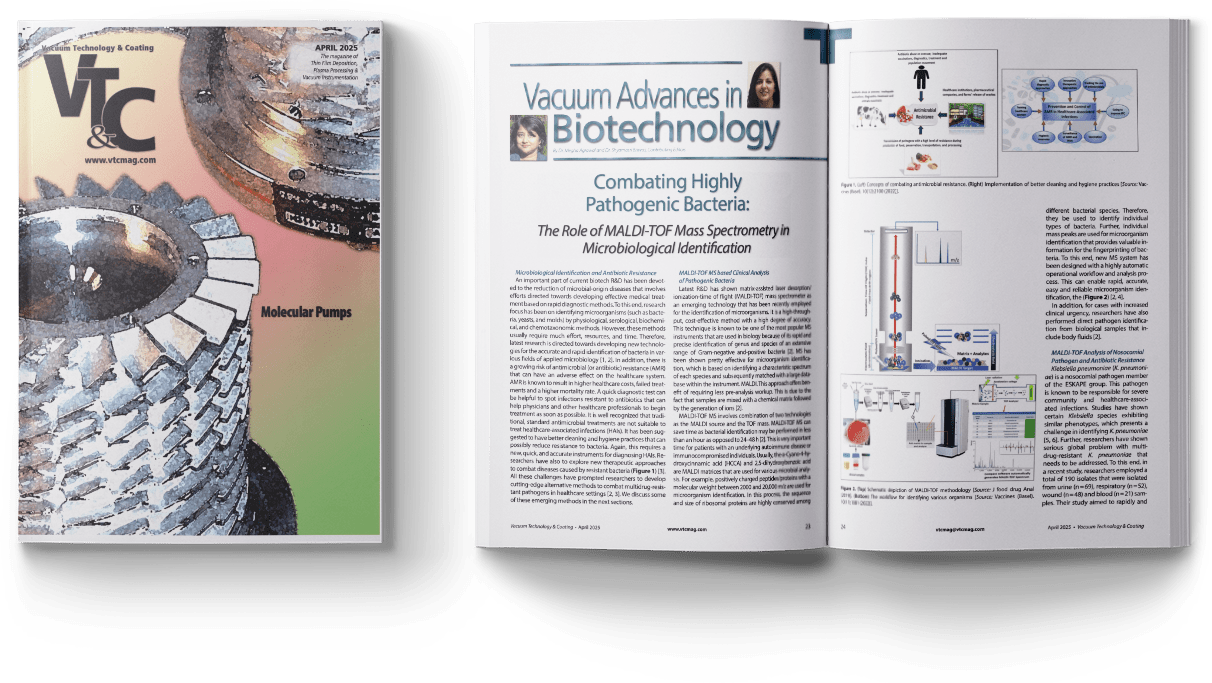
KDF continues to innovate in the field of reactive sputtering with its specially designed and patented sputter sources and the integration of Plasma Emission Monitoring (PEM). (click for more)
Modern electron microscopes can capture incredibly detailed images of materials down to the atomic level, providing valuable insights for materials science. However, they require a skilled operator and can only focus on very small areas at a time. Researchers at the Department of Energy’s Lawrence Berkeley National Laboratory (Berkeley Lab) created an automated workflow that overcomes these limitations by allowing large amounts of data to be collected over wide areas without human intervention – and then quickly transferred to supercomputers for real-time processing. (click for more)
Achieving sub-micron feature sizes on a production basis requires an understanding of the complete processing environment including the vacuum reactor itself. Molecular level chemical contamination demands that all processes factor in the vacuum environment. The vacuum system base pressures are a critical parameter in determining the environmental contribution to wafer contamination. Actual processing levels may be decades above the base pressure, but the base pressure establishes the environmental noise of the system.
American Elements CEO explains the current state of rare earths & China
Since 2000 Vacuum Technology & Coating Magazine has been the industry's leading source for the latest articles, news, and product and service information. Below we describe some of the terms that you will find in a typical issue of VT&C.
Vacuum Coating (Vacuum Deposition and Thin Film Deposition) is the process of depositing a film or other material atom by atom or molecule by molecule onto a surface in a low pressure environment or vacuum.
Physical Vapor Deposition or PVD refers to vacuum deposition methods which involve the material (which is being deposited) going from a condensed phase to a vapor phase and then to a thin film condensed phase. Sputtering and evaporation are common PVD processes.
Sputtering refers to a type of process used to deposit thin films and employs a plasma to bombard and eject atoms from a target source.
Evaporation refers to the heated source material being evaporated in a vacuum. Vacuum allows vapor particles to travel directly to the target object, where they condense back to a solid state. (called a Deposition Source) refers to a type of process used to deposit thin films and employs a plasma to bombard and eject atoms from the target source (called a Deposition Source).
Vacuum Hardware refers to the types of hardware and components that are used in the vacuum process. There are many types of hardware used in this process, some examples are flanges, fittings, seals, valves, and chambers.
Thin Film Metrology involves determining the optimal thickness, composition and/or condition of a coating through various techniques and mathematical calculations.
Gas Analytical Systems are used in the analysis of residual gases within a low pressure environment or vacuum.
Vacuum Pumps are devices that remove gas atoms and molecules for the purpose of leaving behind a partial vacuum. Some examples of types of vacuum pumps are rotary vane pumps, diaphragm pumps, and scroll pumps.
Every issue of VT&C includes a product showcase focused on a specific topic relevant to Vacuum Processing, please see our editorial calendar which lists the topic for each issue.